Episodes
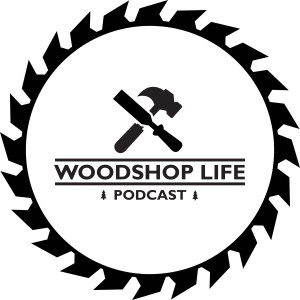
Friday Feb 07, 2025
Friday Feb 07, 2025
This Episodes Questions:
Brians Questions:
I am making a toy box for my grandson out of white oak. The dimensions will be 38” width, 18” depth, and 30” high. The front will be 4/4 quarter sawn, while the back and sides will be 4/4 flat sawn lumber. I plan to attach the front and sides, and the back and sides via dovetails. Since quarter sawn wood will move less than flat sawn, should I be concerned about the wood moving at different ratios? Also, can you recommend hinges that will prevent the top of the toy box from crashing down on my grandson’s fingers?
Mike
My question concerns the router table that I built myself out of out of MDF and 2x4s last year. I'm pretty satisfied with it overall. I am by no means an expert, but I'd have to say having the router in a table seems to be roughly 1,000% more effective than using the router freehand.
Having said that, I've been struggling with the fence, especially When I'm trying to edge join a board. My approach for securing the fence has been to clamp down each end of it with a trigger clamp, placing an additional clamp on the support frame or what have you at the rear of the router table. I've included a picture of my setup for this as well for clarity's sake.
Here's the problem I'm running into: I position the fence, clamp it down, then check it again to make sure it hasn't come out of alignment. When I initially begin running boards over the router table, it works great. However, before too long, sometimes as soon as the second board, I find the fence is no longer properly aligned. When I check it I always find that the fence has shifted back towards the far end of the router table, usually by a 32nd of an inch or so. As you are all aware, this small difference has a pretty significant impact on how my boards come out, particularly when edge joining.
My assumption is that this shift is due to my exerting pressure against the fence while feeding material through to keep the work piece tight against it. Do any of you have any suggestions regarding how I can secure my fence more effectively? Part of me wonders if I am just applying too much sideways pressure to my work pieces, but I also feel like I am applying just enough pressure to keep it from wandering away from the fence when passing the bit. Zach Owens
Guy's Questions:
I'd also like to hear about your process for organizing your shop space and how often you revisit the layout of your shop.
As a follow-up to each question, I'd be curious if organizing and maintaining a shop are aspects of woodworking that you enjoy? Or loathe? Or maybe just tolerate?
Marc
I think there is a good question about red vs blue. red corner is woodpeckers, the YouTube influencers certified measuring and layout tools. Then there’s the poor humans with affordable blue corner igaging. I believe woodpeckers is rated in their accuracy to .002 inch and igaging is .002 inch. So, I wonder if that .001 would make my skills somehow greater?? I think honestly that having a set of tools that I can use without each being a different measurement, as tape measures often would be. I also think about cost, even with a higher shipping fee due to my location I nearly outfitted my shop with all the marking and measuring tools at roughly $300 instead of $300 for one ruler or square.
Thanks for the ongoing pod cast hope you all have a great year. Paul Mitchell
Huy's Questions:
On the face of wood, there is clearly a right and wrong direction to plane. Going the wrong direction causes gouging, chipping, and/or a time tough pushing the plane across the wood. How do you tell the correct direction to go with the plane, without having to risk messing up the piece by potentially going the wrong direction across the face of the wood with your plane? George
I just made my first attempt at cutting dovetails for a small box with dividers that my wife asked me to make her for work. I cut them using a router table that I made just for the occasion. It went fairly well, meaning that they all fit and there aren't any unsightly large gaps. Starting with test pieces was definitely the way to go.
I did have one issue, however. I'm not sure what the appropriate name for the different pieces of a dovetail are, but when I was cutting the female pieces I kept running into an issue where the router bit would jerk the work piece away from the fence, resulting in a somewhat crooked portion in my otherwise straight dovetail cut. I tried feeding the work piece into the bit from each side to see if one direction worked better than the other, but that didn't seem to help. I know that typically the recommendation is to make several shallow passes, but obviously this is not possible with a dovetail. Do you have any guesses as to what I might have been doing wrong? Should I have been pushing the work piece more firmly against the fence? Thanks in advance for your answers and insight. Can't wait to hear your next episode.
Sincerely,Z achary T Owens
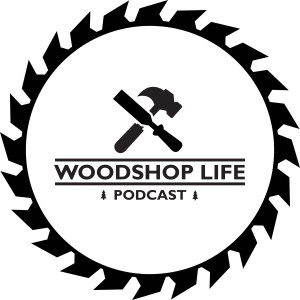
Saturday Jan 25, 2025
Maintenance Routines, Knock Down Hardware, Basic Shop Tools, And MORE!!!
Saturday Jan 25, 2025
Saturday Jan 25, 2025
This Episodes Questions:
Brians Questions:
Hello Guy, Huy, and Sean,
I have two questions. 1) I'd like to hear your thoughts on your workshop maintenance routines. Are there yearly, monthly, project-ly routines to the maintenance and cleaning you do in your shops? Marc
What are your woodworking goals for 2025? Brian
Guys Questions:
Hey Guys,
First, thanks for the fantastic podcast. I always enjoy listening to you gents so much so that I've managed to get through the entirety of your past episodes. A little background: I work in a small space and am consider going with a combo jointer - planer can leave me some room for something else. I am not a a professional woodworker but an enthusiastic hobbyist. Right now I have a bench top 10" jointer (I definitely understand why Guy pretty much hates these things) and a DeWalt 735 planer. I'm happy with the DeWalt, but the jointer can get finicky if it's moved or looked at. I believe I heard in a past episode that Huy is using a Hammer A3-31 jointer-planer combo. Huy - are you in fact using a Hammer combo machine? And if so, are you happy with it? Is the fence pretty solid? If you were to buy again, what else would you consider? My other option is maybe a non-combo mid-price point Powermatic or Grizzly jointer. Any other brands to consider? It's a tough choice - spend more money but use less space or spend less money and use up more of that limited space. Would appreciate hearing from each of you on this topic. Apologies for my long winded questions, but this feels like a big decision.
Thanks again for the excellent show.
Ron
As always thank you for the podcast and sharing your knowledge. This one may be mainly for Guy as I know he’s a proponent of the Lamello Zeta P2. Like Huy I’m a bit of a tool junkie, and can't pass up a new one. I was never happy with my old Porter Cable biscuit Joiner, so I gravitated to the Domino DF500 which has been a great tool. I came across a deal where someone was selling a complete Zeta P2 system so I picked it up. I’ve watched a number of the videos guy posted using the Zeta P2 and so far she seems like a great machine, but now I have some questions that I was hoping you could point me in the right direction:
1) Is there any reason to keep my old Porter Cable Biscuit joiner?
2) I have the knock down domino accessories that I’ve used on some builds in the past. Do you have a guide line or any thoughts on when you would use the Domino vs. the Lamello?
Thanks again, Doug
Huy's Questions:
Hello gentlemen, since you have been asking for questions, here are some for you regarding tools for projects, projects for tools, and tools AS projects.
First, tools for projects. Thinking back my early days in woodworking, there were many times when I would have an idea for a project that exceeded the capabilities of my limited tool collection. Some of these were a basic as ripping a board or making an accurate cross cut. I managed to get by with the most basic table saw that I could afford and an old circular saw. Since a lot has changed in the 30 years since I started, like track saws and set-ups like MFT and Kreg's table setups, what would you guys recommend for the basic tools for someone starting out?
Second, projects for tools. As I started to improve my skills as a woodworker and more tools became available, I felt the need to add tools to my shop. To help justify the purchases, I found myself coming up with projects that would be easier if I had that "special tool/bit/blade." Have you every made a project specifically designed to justify a tool purchase, or is it just me? If so, what was the project and what was the tool?
Third, tools AS projects. A few years ago I started to get more into hand tool woodworking after inheriting some of my grandfather's collection. I also began frequenting a couple of used tool stores in Maine while on vacation where I picked up some vintage panel saws and most of a Stanley 78 rabbet plane. With some cleaning and sharpening I began to really appreciate the use of hand tools and began looking for a used router plane. I don't know if it was just the area that I live in (New England), but there are very few used router planes to be found, and the few that I did find were almost as much as a new one.
Determined to add a router plane to my arsenal I went online, found multiple different options for making my own, and then settled on the Paul Sellers' kit for the hardware and using hickory and cherry for the base. I found out to be a very fun project that taught me some new skills, and I use the tool very frequently. Have you guys done similar projects to make a useful tool that also improved your skills?
Thank you for you time. Joshua
The Black Dog Woodworks
Hello again gentlemen. You guys are the best at answering questions. My third question involves making two 11" by 11 3/4" panel doors that slide left and right in a groove cut into the top and bottom of the frame. The door panels are made of 1/2" MDF but with a 3" wide piece of Poplar that is glued to the top and bottom ends of the MDF. This is to allow for cutting the rabbet into wood instead of MDF. The rabbet will slide in upper and lower grooves in the frame.
I created my own veneer of Walnut in the front face and Poplar in the back face because I'm cheap and the back won't show. Both veneers are 7/64" thick and the long grain runs left to right (same direction of the door travel). I used Titebond Veneer glue and glued both faces at once. I sandwiched the assembly between two pieces of plywood and clamped and weighted the whole thing.
After 24 hours, I removed the clamps and saw that the panel had cupped in the direction across the grain (the same as a 12" wide board would cup). I don't understand why it cupped as I thought MDF wouldn't allow that to happen. I did use too much glue on the walnut side as there was a lot of squeeze-out. I backed off the amount of glue on the Poplar side. Was the veneer too thick? Should I have ran the back face veneer perpendicular to the front face instead of in the same direction? Did the two 3" wide Poplar pieces somehow contribute to the cupping? I am waiting on doing the second door panel until I hear your opinions on this.
Thank you for a great podcast. I hope you all keep it going.
Anthony
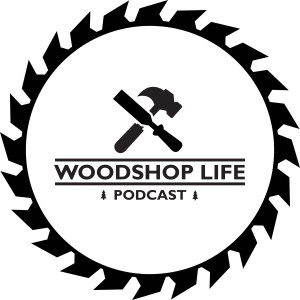
Friday Jan 10, 2025
A Holiday Break!
Friday Jan 10, 2025
Friday Jan 10, 2025
Hello all,
We are taking a one episode break for the holidays and all three of us are dealing with some kind of cold/flu. See you again in two weeks!
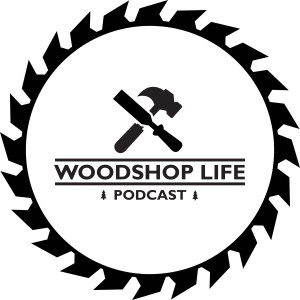
Friday Dec 27, 2024
Making Thin Stock, Angled Tenons, Dust Collector Placement and MORE!!!
Friday Dec 27, 2024
Friday Dec 27, 2024
This Episodes Questions:
Brians Questions:
I'm in the market to upgrade to a cabinet saw that I want to last for a long time. I've been using a Powermatic 64A contractors saw for the past two years that I bought used and have done my best to tune up. That saw still has its flaws though, and it's time to move on. I'm setting a budget of roughly $4000. I want a new saw with a 3 HP motor. 30" rip capacity is enough for me, as I can break down sheet goods using other methods, it will also fit better in my shop. I'm currently considering the Powermatic 2000B or the Sawstop 3 HP cabinet saw. Which one would you choose, and why? What other models would you consider? Love the podcast! Thanks for your advice! Mike K.
Hey guys!
I’ve recently started scroll saw portraits (ex. Newton Makes Art or Scrollsaw Scribbler). So far I’ve stuck mainly to using pre-milled 1/4” stock, but I would like to add some dimension to the pieces and get even thinner stock, down to 3/16” or 1/8”. I recently added a planer to the shop and was thinking of taping stock to an MDF board to thickness the stock further.
So my questions, first do you think this is safe? I have fears going this thin may lead to things getting ripped apart on the planer. Second, is there any other ways you’d recommend getting boards this thin? PS I do not have a drum sander to help with that last bit of flattening.
-Trevor
Guys Questions:
I am a relatively new woodworker. Still learning skills, techniques, and patience with woodworking.
Last year I made a pair of bar stools using cherry wood. It was my first real project of any significance, and overall I am really proud of how they turned out and how they have been holding up to daily use.
This is a two part question because these are the two issues I struggled with the most during the build.
1. I made the legs of the stools splayed, and raked. I used blind mortise and tenon joinery to attach the rails to the legs. Since the legs were splayed and raked, I had to cut my mortise and tenons joint on an angle to accommodate the legs not being vertical. I used a forsner bit on the drill press and angled the table to roughly the proper angle, then used a chisel to square the holes. But I really struggled to do this accurately, especially when using the chisel to square the angled hole. What advice would you give to get precise angles, and to keep that angle while chiseling the holes square?
Part 2. What would you suggest for attaching the seat to the base of the stool? I pre drilled holes into the bottom on the seat and used screws from underneath. You can’t see them unless you foil the stool upside down. but I felt like a bit of a hack doing that and would have preferred to use some sort of joinery instead of screws.
Thanks again for providing the woodworking community with your knowledge and for the great entertainment. Braden
Hey Gents! Canadian listener here, I found your podcast about a week ago and i have been listening every day now. Thanks for the content.
I love the look of pure oil finishes like tung oil but I can't handle how long it takes to dry. I have heard you can thin it to help. Is this something you guys do from time to time and if so what do you thin with / what ratio? Tyler
Huys Questions:
Hey Guys,
As I’m working on building a new shop this summer. I’m getting a little closer to figuring out dust collection for the big machines. I ended up putting two 6” runs in the slab. But I’m stuck on which DC types work best.
I built a large storage shed off the back of the shop that is walled off and the plan is to store the DC, lumber , air compressor, etc.
I know a cyclone with a hepa filter is the gold standard in removing fine dust, which makes sense if the DC is inside the conditioned shop.
But I already have a dual bag setup from Shop fox W1687 (3hp DC with separater and bag filters). I think this setup may get better air movement than the cyclone. And since it’s housed “outside” of the shop I think the filter requirements could be reduced.
Shop specs: 470 sq, all the normal machines to process rough lumber. Jesse
Hello from Australia!
I've been an enthusiastic hobbyist woodworker for about 18 months. I use mostly hand tools except a budget circular saw, which I hate, and I just got a 12 inch bandsaw, which I love.
So far I've build a joiners bench, several planes, including a 52 degree smoother from a broken Stanley no.3. And I'm most of the way through a small bookshelf made from Tasmanian oak.
As you know a lot of Australian wood is hard and can be challenging to work with. My next wood will be Austrian blackwood, which is moderately hard and has a high silica content. But it is also filled with glow and once oiled looks amazing.
I also have some reclaimed floorboards which are some kind of gum tree. I would like to use them at some point but the boards are determined to remain in their current form. They are difficult to work with and if my no.5 plane is not super sharp it will just skip over the wood.
Can you share any tips and knowledge on working with hard woods?
Thanks for the show, I've learnt a lot from it
Kind regards
Jeremy
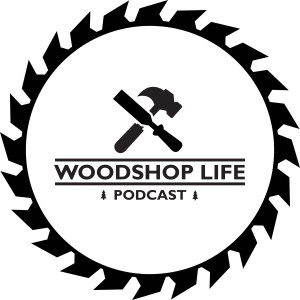
Friday Dec 13, 2024
Jig Making, Too Many Exotics?, Honing Hand Tool Skills and MORE!!!
Friday Dec 13, 2024
Friday Dec 13, 2024
This Episodes Questions:
Brians Questions:
Hola fellas,
Been a minute since I've bothered you, I've been busy with rebuilding my 1000 sqft deck with black locust I am milling from logs. It's taking a while, and most of my families patience with me. I took a detour to rebuild my music studio, so now all my neighbors get to listen to death core metal. I need to mill up this beech tree for a giant dresser but that's a topic for another time. Lot going on around here.
I got a hot one for today:
Some unbridled genius at my kids' day camp decided it would be a good idea for me to teach young children woodworking. I tried to explain that I have a company to run, am really irresponsible with other people's kids, don't know how to keep myself safe, etc. but they're pretty insistent. I talked them down from me being an actual camp counselor, to doing one or two workshops a week with different age groups from 6 up to 12 years old.
I have a ton of scrap that can be used, a box of screwdrivers and crab mallets, 20 little glue bottles, and a bunch of sandpaper. Now I need some projects.
Any ideas? I have the standard bird house / solid wood cutting board / pencil holder type stuff you can find online but I want something more exciting. What else can I do with young kids, that can be glued, nailed, tied, or screwed together from pre-fabricated parts? I want to get them to decorating whatever we make as quickly as possible, I've found with my kids that's when they get really excited.
I should mention the camp has offered to purchase some tools for the kids, and materials, so I'm not limited there, but I think i want to keep power tools out of it. Make me a hero here gentlemen and I will be certain to share the accolades with WSLPC (WLP?). Happy Thanksgiving / Holidays / New Year's. Big Tom
Hello guys,
Is there a material / construction method that I should be preferring for making jigs if I want them to last a long time?
Max Greddie Woodworks
Guys Questions:
I am looking to build a dresser.
Tentatively, I am thinking zebrawood main structure, which I would stain to match a cinnamon-brown stained maple desk that will be sitting beside the dresser.
I am thinking about doing the drawer fronts in Bubinga, which also looks similar in color to the maple and zebrawood, when finished.
The top of the dresser, I was thinking of quartersawn Sapele. Sapele is relatively inexpensive and I love the ribbons and chatoyance of Sapele.
The mirror surround material I am still undecided on, but probably Sapele.
Is this too many wood types on one piece ?
I have a few more bedroom pieces to eventually make and it seems like I risk having every species in The Wood Database in my bedroom, but my last couple of pieces have been Sapele and Khaya, and although I like the look, it's time for a change. Stephen
It's rather simple or basic, actually. When I first entered this school shop, it had been a while since there was a dedicated teacher. As such, some of the equipment was in need of some maintenance attention. Specifically, the tops or working surfaces of various pieces of equipment (3 table saws, planer, jointer, sanders, band saws, etc. - hopefully you get the picture). I purchased a can of Johnson's paste wax, a couple of wax applicators and went to town. Now, in the present, I can see the bottom of my can of wax - AND THERE IS NO JOHNSON'S PASTE WAX TO BE FOUND (except for certain websites that want an near fortune for the stuff). I know there are other products that companies have dedicated time and money to develop just for this purpose (various sprays and the like) but am wondering a couple of things. Should I, because according to the company, it isn't coming back so I should just embrace the change and just use the new stuff - OR - is there a similar product that can accomplish the same objective and is a simple solution? Will any paste wax work? I have seen a product called Shop Wax made by Bumblechutes and am wondering if that will work. I understand that I want to provide work surface lubrication without imparting anything to the surface of the material that could later hinder the application of finish.
Speaking of finish, that will be my next question - I understand that you guys just LIVE for answering questions about finishing!
Warm regards and keep up the great work,
Rob Harrison
Huys Questions:
I've enjoyed your many insightful answers.
We are having our first grandchild in a couple weeks (yah!!!)
My main Fall project is to make a high chair for this little girl. She won't be in it until early in 2025.
I have my in-laws old high chair that they used for their children and the first couple grandchildren.
I am going to use it as an inspiration for a new chair.
However, I think having a set of modern plans would also be helpful.
In my visiting the local Rockler and Woodcraft stores I have not found anything useful.
I've also search close to a dozen websites.
[Rockler.com, Woodcraft, NewYankee, fixthisbuildthat, wood, etsy, woodsmith, shopnotes, popularwoodworking, amazon, ebay, etc...
I have not found anything very useful.
Do you all have any suggestions to improve my search for useful plans?
Thank you, Chuck
Love the show and I really enjoy listening to you all give your unique perspectives to people's questions. I've learned a great deal over the last year or so since I found your podcast and wanted to say thank you, so...thank you!
You asked for questions, so I thought I'd submit something and see what you all thought. It's a strange one, so hang on!
I started woodworking during the pandemic and fell in love with it. I had zero experience but after watching some YouTube videos I made a few shelves, then some cabinets, then moved to building furniture.
Recently, I thought I'd try to elevate my skills and build more elaborate pieces using joinery like dovetails using hand tools, chisels, hand plane, dovetail saw, etc, and have been really enjoying the challenge. I have forced myself to use my hand tools almost exclusively to accelerate my skill building with some success, but I am looking to speed up the learning process. To that end, I was hoping that you guys could suggest any "drills" that I can use to improve the basics of hand sawing, chisel work, and hand planing.
I tend to break down a task into its sub-components and work on mastering each of those skills to improve as fast as possible. For example, hitting a baseball, you can break down into small sub skills like loading, stepping, indexing, swinging, follow through, etc. I'd spend hours on getting each piece perfect and then bring it all together for an excellent swing.
Anyway, I was looking to apply the same process to hand tool skills, but I don't know what I don't know, hence the (way too long) question.
For example, before I attempt to saw a tenon or dovetail, I'll put a bunch of lines on a scrap board and practice staring a cut on a line a bunch of times, then make the cut down the lines, or next to the lines, etc, just to get warmed up before I cut my work pieces. Chisel work is brand new to me and where I really need help, so I'd love to start there, but welcome any sawing or planing drills as well. Any suggestions on skill building exercises I could use to level up?
Sorry this question is so long, and I hope that it makes sense. Feel free to edit this down if you do happen to use it on the podcast, I know it was long and rambling.
I appreciate any help you can offer as well as all you do for the community.
Cheers,
Tobias
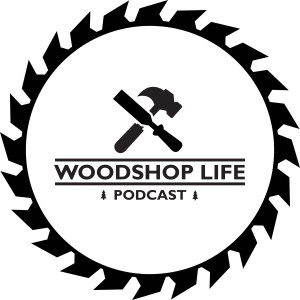
Saturday Nov 30, 2024
Workbench Stability, Drum Sander Woes, Veneer Glus and MORE!!!
Saturday Nov 30, 2024
Saturday Nov 30, 2024
This Episodes Questions
Brians Questions
I was at a big box store the other day getting a new toilet. As I passed the lumber section, I saw what looked, from far away, like a piece of walnut. On closer inspection, it was a piece of rainbow poplar in with the ugly, green big box poplar for the same price as the regular poplar. Of course I bought it. My question is: was that awesome and, if so, how awesome?
Thanks, Sincerely, American Bob
Hey Gents! Canadian listener here, I found your podcast about a week ago and i have been listening every day now. Thanks for the content.
I started woodworking this year and just built a new workbench using Paul Sellers plans. It has a laminated 2x3 top with a well so it's quite heavy. I use both power tools and hand tools. The main point of making this new bench was to make it heavy so it doesn't slide during hand planing, but it still slides!!! Any tips on how to prevent workbench slide?
My workbench needs to float away from the wall so i am looking for a solution that isn't "put something behind it".
Any tips would be greatly appreciated!
Thanks again! Tyler
Guys Questions
I have a question regarding the drum sander. I only swear while doing two things, playing golf and using my drum sander. I bought a new Supermax 16-32 and had nothing but problems with it and had to send it in for warranty repair. I sold it and upgraded to a Powermatic PM2244 which I believe Guy has. I definitely have had better luck with the Powermatic but still have issues with burning at times. I do make end grain cutting boards for friends, family and donations. I know the end grain is extremely hard. I take very shallow passes, usually .002 to .004 per pass running the conveyor at 4 FPM and no matter how careful I am I still will get burning and grooves. It doesn’t matter the grit of the sandpaper. I’ve experimented with feed rate with no luck. I know the glue does create heat and builds up on the paper so I clean the sandpaper often. Do you have any recommendations or should I start a swear jar to raise money for charity? Thanks again, Matt
Good evening, gentleman! Thanks for this amazing podcast and all the info! I had a quick question on blades for a cheap table saw.
I used to use the newer delta contractors saw (miss it so much..best saw I've used) unfortunately, had to down size. So I'm back to my ryobi cheaper saw. I keep the blade and adjustments true, so it cuts well....for what it is. Yall mentioned a few weeks back, thin curf blades vs regular 10".
Question: I use a smaller circular saw blade in my table saw. Have you? Have you noticed more power and better cuts? Because I have. In all saws I've used. Would you recommend using a smaller blade in a cheap table saw to get more power to the blade? I'm just kinda wondering your thoughts on that. I'm a one man backyard shop that mostly is building cabinet doors out of poplar and barn doors out of pine, and poplar. Thoughts? Thanks in advance! Keep up the amazing programming! Crafted Carpentry Canada
Huy's Questions
EH gentlemen from the Niagara region in Ontario Canada, been listening to your excellent podcast for some time now and thoroughly enjoy it so thank you for that. My question concerns urns and specifically how it seals.
For context, my wife's grandmother has recently passed away and I was asked by my wife's family to make her urn.
I don't own a lathe but I very carefully using an angle grinder with a shaping disc, orbital sander and an excessive amount of hand sanding created a typical tapering cylindrical urn that is fatter about 1/3 of the way down from the top, tapering upwards and downwards from there and I used segmented layers to achieve this.
The urn is made of blood wood and has soft maple accent rings.
The lid I created was a simple circle that I used dowel pins and magnets to secure it to the top of the urn.
I am extremely happy with how the urn turned out and how the lid looks on the urn but I am not 100% happy with how the lid I attached and sealed.
So after all that my question is: how would you guys go about creating and attaching the lid? In my research I did see most urns have a threaded component on the bottom of the urn and that's how they seal.
Apologies for the long winded question, any insight would be greatly appreciated. Thanks James
I have a question about types of glue for veneering projects. In the past I’ve used Unibond 800 with good results. The problem I have is the very short shelf life for someone who does 1 or 2 veneering projects per year. Are you aware of any other solutions with longer shelf life without resorting to some PVA glue?
Thanks and keep up the good work! Jeffrey
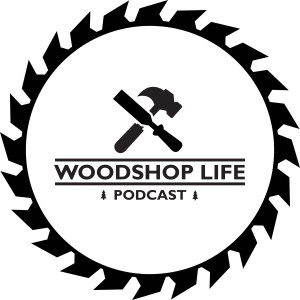
Friday Nov 15, 2024
Friday Nov 15, 2024
This Episodes Questions:
Brians Questions:
I have a question on wood storage I have a smaller shop and lots of tools so wood storage space is tight. I purchase my wood based on what I have planned for the next 2-3 projects and try not to stock many extra boards. I store them on end leaning against an outside wall. I often clamp several boards together to help avoid bowing. So far no problems but I am fairly new to full time woodworking as I retired 2 years ago.
Do you see any problems with this method that I haven't experienced yet? With the cost of hardwood lumber I don't want to be surprised with wood that I cant use. Thanks Dean
I’m just finishing up building all the cabinetry for my Seattle home and decided to take on the interior doors as a new challenge. I’d like the doors to appear as if they’re made from 5-6 vertical wood boards, with a small 1/8” kerf between each board (I’ve attached an inspiration image). I know that a large glue-up of solid wood would expand and contract undesirably for a door, so here’s my current plan to keep things stable:
I’m planning to veneer 1 1/2” by 5 1/2” TimberStrand engineered studs with 1/8” shop-sawn veneers in a vacuum press, ending up with a 1 3/4” stile. Then, I’d edge glue the 5-6 stiles together, reinforcing each joint with Dominos. Once glued up, I’d add the 1/8” kerfs with a track saw.
My questions are as follows:
1. Would you recommend using the largest 14mm x 140mm Dominos between each stile, and if so, how many and at what spacing across each 8-foot section?
2. Do you have any tips for gluing the doors up flat?
3. Does this seem like a viable method to achieve a flat, stable door with the look I’m after, or is there another approach you’d suggest?
Thanks for your input and for all the time you put into creating such a great show! Best, Sam
I would like your thoughts on the depth/ratio you prefer for cabinet or bookcase dado's for shelves - for example if using 3/4" plywood for a cabinet, or 3/4" hardwood a bookcase. It is my understanding that 1/4" is a good depth overall. I am planning on building both some cabinets this fall, but my current project that I am preparing for is a hardwood Scandinavian bookcase. I am considering fixed shelves installed via dado. Each shelf will have an offset vertical shelf divider, also installed via dado. John Sanchez
Guys Questions:
A few years ago I refinished our oak dining table. It may be close to 100 years old. My mother used it in her youth, and I am now 61 years old. To refinish it, I used - sorry to say - MinWax - stain and water based satin Polycrylic. We use this table everyday for any meal we eat at home. Well, the finish has gotten gummy where I rest my arms on the table. Now I need to refinish it again.
I had recently applied Osmo Polyx-Oil hard oil wax on a guitar neck that I finished, and really like it. Would this be a good, durable finish for an oak dining table that sees daily use? And not gum up again?
Thanks, David Vespoint
I am contemplating a (non-epoxy) dining table build using some soft maple slabs I have acquired. I will mill the slabs into as wide of boards as I can and glue them up and get them surfaced so that my final dimensions will be about 84”x35”x2.5”. I want to add a fairly significant under bevel, leaving about 3/4” on the edge and cutting at a 16 degree (or 74 degree, depending on how you measure it) angle, so that the bevel ends about six inches from the edge on the bottom of the table. My question is: How the heck do I do that? I have a table saw, but I don’t think I’m lifting this whole tabletop and running it through my table saw (the blade isn’t long enough anyways). I thought about getting a track saw, but it turns out they use dinky little blades. Do I make an angled sled for my router? Do I use my 4” handheld power plane? Is there another solution I am not imagining? Thanks! Jon
I'm building a couple of nightstands for my daughter based on an image she gave me. She needs the diameter of the round top to be between 15 and 17 inches. The legs are 2 panels, one is 13 inches wide and one is 10 inches wide, the 10 inch wide panel will be cut at an angle and attached at 90 degrees to the 13 inch panel. I made a template with MDF, and the table works fine with the top width of 16 inches.
I'll be using knotty alder and I can get it in 5" 7" 8" and 10" widths. My question is: when I get the boards to glue together to make the correct sized panels for cutting into the legs and top, should I use all the same widths of boards I buy, or can I vary the widths to use the wood most efficiently? It's an aesthetic question more than an functional one. Do table makers use the same width of boards for the top and the base of tables? If you don't, does it look odd?
If I could attach a photo this might make more sense. Thanks! Trish
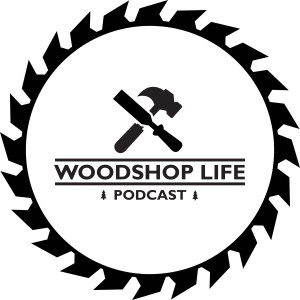
Friday Nov 01, 2024
Dye Colors, Mitered Boxes, Glue Creep and MORE!!
Friday Nov 01, 2024
Friday Nov 01, 2024
This Episodes Questions:
Brians Questions:
Hello Guys,
Love the show so much great information. I have recently got into scroll sawing. I am a comic book fan and I want to start scrolling the comic book art that I love. As you may know comic book art is very colorful. My goal is to start getting enough exotic wood to try and cover as much color as I can. In the mean time I would like to start using stain to color the woods. Are you all aware of any stains that have a good color spectrum.
Thanks
Korey from Independence KY
I am looking to build a shop building on my property. What is the minimum square footage you would recommend for a home hobbyist? I will have a miter saw, router table, table saw, and eventually a planer and dust collector. And of course a work bench with a saw vise.
I have plenty of room on my property, so that isn't a limiting factor. My biggest concern is not spending money that I don't need to on a building that is larger than needed.
What are some things you recommend that I plan for when building? Power outlet locations and qty, ceiling height, lighting type, etc.?
Thanks in advance! Kyle
Guys Questions:
I know you guys have referenced putting shellac under water based finish so you can have the richer look in the wood but ease/quick timeline of water based. I typically use an airless sprayer to apply General Finishes High Performance. I have some projects with walnut that I would normally finish with Arm-R-Seal to get the rich walnut tone. Id like to try the shellac coat first and then High Performance on top. I was wondering what is your standard application practice when you do this. Do you apply shellac (by hand or spray) and then wait a few hours/a few days/a week? Thanks for the advice and looking to avoid any pitfalls in the process being that Ive never done it before.
Thanks and keep up the good work on the podcast.
Pete from Uncarved Block Woodworks, Madison, WI
Do you have any tips for glueing up mitered-corner boxes to ensure they are square/plumb, etc.? I've had a hard time with this. Thanks David Vespoint
Huys Questions:
My local Rockler shut down and I found myself purchasing the Dark Half Tung oil from the real milk paint company at a steep discount. Never used the stuff but I’ve heard that dark tung oil can help give cherry a patina look without aging. I’m wondering if it can help walnut preserve its dark color over time?
Tung oil is supposed to be a pretty durable finish on it own. Have you guys tried using it as part of an arm r seal mix?
Thanks again for the help! Jose
All of my furniture pieces seem to have glue creep on all the table tops and panels. I switched from using titebond pva to titebond hide glue thinking this would solve the problem. On some newer pieces I built with the hide glue, I can now slightly feel the glue seams after a few weeks. The tops all have biscuits for alignment as well. Could this be a matter of temperature and humidity change from my shop to my house? About 40% humidity in my shop through the use of a dehumidifier. Temperature ranged from in the 50s this past winter to now it's in the 80s. Would you sand the seam lightly with 0000 steel wool or very high grit sandpaper? And any tips for future builds to avoid this again? Thanks guys! Jeff
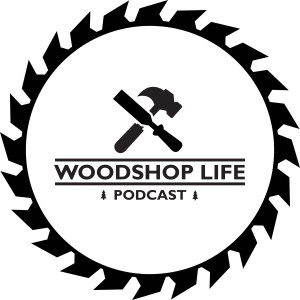
Friday Oct 18, 2024
Miter Station Size? Catastrophic Failures, Outdoor Finishes and MORE!!!
Friday Oct 18, 2024
Friday Oct 18, 2024
This Episodes Questions:
Guys Questions:
Gentleman, Chris here @custom_by_chris on Instagram. My shop is a single car garage roughly 11.5’ wide by 22’ long. I’d like to build a miter station along the front wall for my Kapex. Will I regret confining myself to that 11.5’ width? I would position the saw so I have at least 8’ of cutting capacity to one side. I am not doing regular trim work so don’t frequently deal with long stock. Lastly, when designing and building the miter station what features would you consider must-haves or things that aren’t necessary? It’s easy to get sucked into the YouTube rabbit hole of miter stations so please guide me back to the light. Chris
Zach from Minnesota here. I recently constructed a box using box joints for the first time (thank you, I hold the applause.) As the tutorial by wood magazine suggested, I cut the fingers a little long with the intention of trimming them later rather than risking them being slightly too short. I have come across numerous suggestions regarding the best way to trim flush these protruding fingers, and as with most things to do with woodworking every suggested method also includes a comment claiming that following any of the other suggestions will ruin my work piece. What method do each of you prefer to use when flush trimming your box joints? Thanks in advance.
Sincerely, Zachary T Owens
Hi Guy and other guys,
Thanks for the great podcast. I have learned a lot from all the great content you put out. I really appreciate your advice and perspective. I have a couple questions I was hoping you could answer.
Recently I was rubbing a beeswax and tung oil finish on a little box I made for my mother in law. I was using a white scotch bright pad. I guess I didn't softened one of the corners enough because the pad caught the grain and torn out a little piece of edge. My question is what do you do if something catastrophic happens while finishing? Do you sand it back repair it and then finish again? Do you have to sand the whole thing back or just the piece you are repairing? Or is there some trick to repairing finished wood? Or do you just trow it in the fireplace curse a lot and start over?
Thanks. Keep up the great work. Jon Moch
Huys Questions:
Hey guys, longtime follower and still enjoy listening to the podcast. Guy, it seems like you’ve fallen out of love with woodworking a bit and moved onto 3d printing? Is that just because you’ve been doing it forever haha? Always good to have a change.
I wanted to ask you guys about pigmented conversion varnish. I often hear you talk about it and I’ve never heard of it mentioned here in the uk across the pond, the only thing I can find online is it’s potentially the same as what we call acid catalyst? Is it dangerous to spray? Here in the UK acid catalyst (or commonly called AC) is quite toxic and you have to be in a proper booth with serious fume extraction and prober PPE respirator. Is this the same stuff? I’m guessing a pigmented conversion varnish would be a paint finish? Such as a solid colour? Any info would be great.
Keep up the great work guys, Mike
Hey guys thank you for all the information in the podcast and your previous answers to questions. For the most part I make sawdust. I build some furniture pieces, picture frames, boxes, etc. I also build some shipping crates for my real job which helps offset some of the cost of this hobby. The crates use 4x4, 2x8, 2x10 & 2x4 construction lumber and plywood. I've been using a sliding compound miter saw to cut up the boards. I'm reorganizing my garage and was thinking of selling the miter saw and going back to a Radial Arm Saw. I do not do any type of trim work or anything like that. Am I making a mistake wanting to go to the radial? It would just be for breaking down the boards to length. Thanks, Doug
Hi everyone,
Pretty much a novice woodworker with some questions on sapele. My primary question: I have a sapele front door that I inherited that has a finish that has not done well even in dappled sunlight. Fortunately, the door is completely structurally solid, so no repairs needed there. But my question is about how you would refinish it? I kind of like the look of a Danish oil or tung oil with a really solid coat of Total Boat marine finish to protect it. I have also seen people use Eipifanes as a protectant. But with little experience, I am guessing what the outcome will be. I would love to hear the team brainstorm what options I have to both enrich the beauty of the wood and the protect it. What should I optimally do to produce a nice piece that will last with regular care. Any suggestions on products?
More generally, we have some sapele accents in a refinished kitchen. Nothing too fancy or complicated - panhook bars and similar. I would like to build a few more simple pieces. Any thoughts on working with and finishing this type of wood from a broad perspective?
Great podcast. I love how you name brands and don't beat around the bush on advice. As a "maybe I can do it someday" woodworker, I find each episode valuable! Thank you. George
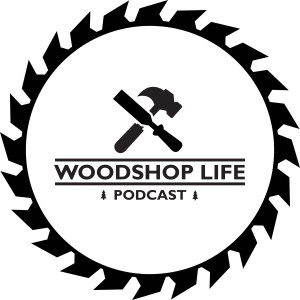
Friday Oct 04, 2024
Cheaper Tools?, No Tablesaw?, Glues in the Shop and MORE!!!
Friday Oct 04, 2024
Friday Oct 04, 2024
This Episodes Questions:
Brians Questions:
Hey guys! Another quick question that I get from others in our field. And I'm interested in your input. What making basic shaker/frame and panel cabinet doors, I use the big box, larger ridged router with the FREUD T&G bit set. I'm tired of cutting the tongues and having blowouts..even when using a backer board when running the rail through the router. I've leaned in to using the BEADLOCK system from rockler. It's been great so far. Would you suggest that loose tenon joint, or stick to the TONGUE in the groove? For durability? Crafted Carpenter
What are some tool under $50 that you (or listeners) love. My examples:
-The Rockler or Milecraft center marking tool
-Temtop S1 Indoor Air Quality Monitor (cheap, accurate, see what’s actually happening in your shop instead of guessing)
-Any router coping sled
George
Guys Questions:
Hi guys
In two pervious shows you mentioned two things.
One. You would give up your table saw in favor of a band saw. The question is what can you do on a table saw that you can not do on a band saw. The only thing I can figure is a Dado joint.
Many thanks,
Paul Mitchell
Oki Mitch Crafts
Good day gentlemen
Long time listener (3-4 years) and still feel your the best woodworking podcast. I build a variety of wood project from band saw boxes to use up scrap pieces to some furniture.
I have a Domino DF 500 and use it often. You talk about a biscuit joiner being a different animal and used for different things. Can you give us examples where a biscuit joiner is the best choice? The examples may answer this question for me but do I need a biscuit joiner? Which brand(s) would you recommend?
Thank You Dean
Huys Questions:
Where do you purchase your shellac flakes? Do you use unwaxed? Thanks Mark Moeller
Hey guys. As always, appreciate the podcast and the information shared.
I thought as a topic you might discuss what glues you keep on hand (types more than brands) as well as what specialty glues you’ll acquire for a specific project or technique.
For example, I keep regular wood glue (partial to Gorilla Wood Glue) for most usage, but I always have liquid hide glue for any sliding joint, like dovetails or box joints. I keep 5 minute epoxy and CA glues, but use them less often (and often wish I hadn’t because they’re usually to fix a mistake). Thanks again.
Peter