Episodes
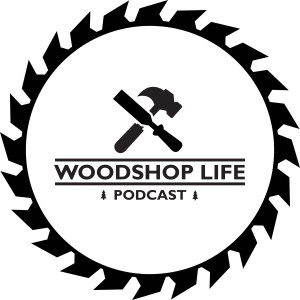
Friday Jul 14, 2023
Shop Built Jigs, Woodworking With Children, Finding Inspiration and MORE!!
Friday Jul 14, 2023
Friday Jul 14, 2023
Brians Questions:
Every time I make a jig I struggle to get the fence square. How do I do this properly. Is this a common problem amongst new woodworkers? Love the show guys keep it up!
Johnny
This is Ben and I’m 8 years old. I would like to make a pocket knife with my dad. What suggestions do you have for making one?
Ben and Nathan
Guys Questions:
I recently found your podcast and have been binging it while in the shop. Guy, I was quite surprised to learn about your passion for 3D printing and various tinkering in his shop. I share the same passion for tinkering that extends beyond woodworking. In my shop I get almost as much satisfaction in discovering/creating a jig or tool to complete the job as I do in the actual finished product. My biggest “tool” build has been the ‘Mostly Printed CNC machine’, which is good enough for cutting various templates or basic v-carves. I can’t justify the price tag for an off the shelf machine to do that work when this one is good enough for me, at least for now. But I don’t think I could ever make something like a dowelmax, when I can buy a quality tool for relatively cheap. Apologies if this has been asked before. My question is about shop built tools and jigs vs. store bought. From your perspectives, with quality and cost in mind, what tools should be purchased off the shelf and what tools can be or maybe should be shop made? (Crosscut sleds, planer jointing sled, flattening jigs, clamping jigs, mobile bases, router tables…the list goes on and on). For reference I’m very much a hobbyist making stuff for the house or family and friends, while selling a piece here and there. So I do not work under any form of deadlines other than those imposed by my wife. Additionally, this is my creative outlet, I’m a gear design engineer the other 40 hours, this is my opportunity to make what I want to make. Keep up the great work!
Caleb Gurd Gears & Grain Woodcraft
Hey guys. You have been kind enough to answer a few of my questions in the past so thought I would throw a couple more your way. I have two questions which fall into the category of finishing. Number one - I'll be building a coffee table out of walnut which is a mix of heartwood and sapwood. I would like to find a way to blend the color of the mixed wood together. If I use a walnut dye on the entire project will the color of the heartwood and sapwood blend together and provide a uniform looking finish? If dying the wood is the solution can you recommend a brand of dye? Should the dye be oil or water based given that I'll likely use an oil based clear coat. I have never used dye in the past so any tips will be helpful. Answered - Second question. Our cherry wood kitchen table, which measures 36"W x 48"L, needs refinishing. I believe the original finish is an oil based pre-catalyzed lacquer. I'll be refinishing just the table top which has several scratches and shallow dents measuring up to 1/16" deep. The legs are painted black so no need to match the color of the top with the legs. Can you recommend a method for removing the original finish? I don't own or have access to a drum sander. Also, can you recommend a durable oil-based finish for refinishing the table top? Is spraying the preferred method for such a large surface area? Or, will a wipe-on poly do the job? Thanks again for all your help and expertise.
Jack Francis Geneva, IL
Huys Questions:
Hello fellas. Thanks for the enjoyable podcast, I've been listening for months but finally asking a question. Where do you look for inspiration when it comes to design for furniture pieces? Any particular magazines or books you like to reference when coming up with designs. Not necessarily looking for how to's , but more on design and style. Thanks again!
A. Torres
Kind sirs- Wonderful job etc. and I hope this finds you well. I posit this question knowing full well that I "overthink things" (according to Guy), even though I am "really intelligent" and have "design style" (according to Huy, your Tom Fan Club membership package is in the mail, including a life-size Tom cutout, suitable for posing with for social media photos.) I need a second desk for a backup office when my in-laws visit. I have a nice 2.5" thick ambrosia maple slab about the right size, and a couple of 4' long, 6" x 8" pine posts. My idea is to wedge-mortice the posts through the slab to create two 30" legs, and then mortice those into the 18" offcuts to make wide "feet". Think two upside down capital "T" going through the slab 3' apart. Would this construction method obviate the need to consider wood movement, since I only have one point of contact between the pieces? My understanding of wood movement is that it is the constraining of movement that can cause issues; in this case I can see the mortices getting 1/16" wider in the winter but if they're wedged, who gives a care? Or, should I hide the mortices and give them a little wiggle room to avoid splitting if the legs swell? Would pine stretching, crack maple? There I go over thinking things again. But thank you for humoring me. I await your answers with bated breath -
Tom the Bomb Figura
No comments yet. Be the first to say something!