Episodes
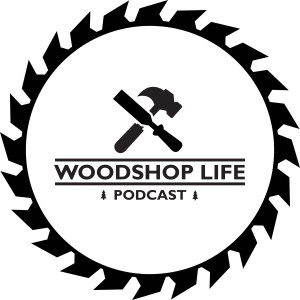
Thursday May 19, 2022
Episode 97 -Solid Slab Tops, Our Inspiration, Alcohol in California & MUCH More!
Thursday May 19, 2022
Thursday May 19, 2022
Support us on Patreon: https://www.patreon.com/woodshoplife
This episode is sponsored by: Shaper Tools, makers of Shaper Origin
Sean
1)Hey guys,
Thanks for all of the knowledge you guys pass on over this platform, it’s great being able to learn from others more well versed in woodworking than myself, especially when it seems that serious hobbyists are few and far between where I’m at. My question is about shellac, which it seems you guys talk about every other, if not every, episode. Because I live in California, denatured alcohol cannot be purchased, even through Amazon. I’ve heard of people using Everclear as a substitute for denatured alcohol, but as research shows, everclear looks to be banned in California as well.
What else can I use to dissolve these shellac flaked ?? Thanks again for the sick content, Tyler
2) Before I ask my question, I just wanted to thank you for your feedback on my last project. The advice you gave me about the box I was working on was perfect. Thank you! Hoping to get your input again.
I have about $1,500 to spend on a bandsaw. Resawing is the priority. Bang for the buck is important, but in this case I could be convinced to set aside another couple hundred or so since I think that the "buy once, cry once" approach could be worth it.
If I remember correctly, Guy has a Powermatic, and I remember seeing Sean's YouTube video about the Hammer. Not sure what Huy has. Regardless, I'm very interested in your thoughts, whether you like what you have, and whether there are other options that I should consider.
Thanks again for a great podcast and for being so generous with your experience. I'm a big fan. Keep them coming! John
Guy
1) What is the most challenging project you've ever completed? What made it challenging? How did you approach the problem-solving required to overcome the challenge? Help us listeners get "in your shoes" and learn from your approach to tackling challenges in woodworking by providing a specific example from your experience. Thanks for all the insights you continue to share on the best woodworking podcast in the universe!
From the other side of the wall, Brian Schmidt
2)You all are an inspiration to me and have always given honest legitimate answers to thousands of questions through the years for so many folks. I’d like to know who was an inspiration to you as you were growing as a craftsman? Especially Guy since he came up in the trade before the internet and social media. Secondary question if you had the chance to meet or learn from one craftsman, who would that be? Brent Jarvis
Huy
1)Kind sirs-
After my last couple of diatribes I'll endeavor to keep this question brief. My wife is a lovely, patient woman and for Valentine's Day I would love to make a pair of nightstands she's been hinting at for a while. Of course, I would have needed to start those two months ago to have any chance at making February 14th. But maybe for next year, with your help.
I'll be making these out of some walnut scavenged from the power company clearing lines. I took two roughly 18" long x 24" diameter logs, and hand-ripped them into rough parts (1" panels, 2" leg stock) about 18 months ago with this in mind, they've been air-drying since.
My conundrum is that these logs are from BRANCHES - the actual tree, still standing, is about 6' in diameter. So for nightstands, wanting a roughly 16" x 22" top, though my inclination is to use the nicest "slabs," maybe get a little sap wood in there, my gut tells me that will look nice for a year and then end up like Sean's cherry table panels, especially because they're air-dried. In your esteemed opinions, should I further rip the slabs into dimensional lumber and then glue up panels for construction? Aesthetically, I could probably use some "traditional" furniture, my wife says the house looks like the Keebler elf village already, we have a 14' long 4" thick live edge mantle, all maple trim with walnut plugs, and I use interesting off-cuts to trim windows.
That was brief, for me. Thanks Tom
2) Thank you so much for taking the time every two weeks to produce this outstanding podcast, which I have thoroughly enjoyed, and have integrated many of your ideas and tips into building my shop and developing skills as a woodworker.
I am in need of an outfeed table, and also a stable, dead flat assembly surface. I think that Huy's "MO/AT" is a terrific solution, but I have a few questions.
I know that the torsion box portion is based on Ron Paulk's popular workbench, which includes the dog holes (that I really want to utilize for clamps, etc.), and the interior storage space. Also, the removable hardboard surface, with its reference dowels, is a great idea that requires access inside the box.
However, I have watched torsion box build videos by Guy, Steve Johnson, Marc Spagnolo, and others, and their designs all differ in that they are thinner, and have a much denser array of "honeycomb" grid elements, which suggests to me a greater chance of remaining dead flat. But of course, they do not allow for meaningful use of dog holes, or interior access.
So I am looking for the best compromise design, one that allows the dog hole array and all of the clamping options, but also has the best longevity for staying flat. Is there a best height, best grid layout configuration that I can aim for? I'm thinking that between you three engineers, the perfect solution will be forthcoming.
Thank you, and please keep up this very much appreciated podcast! Best, Tom Stanley
No comments yet. Be the first to say something!