Episodes
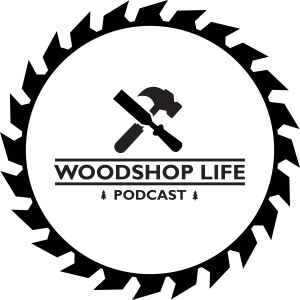
Thursday Jul 28, 2022
Thursday Jul 28, 2022
Support us on Patreon: https://www.patreon.com/woodshoplife
This episode is sponsored by: Shaper Tools, makers of Shaper Origin
Sean
1) How often should I be cleaning my planer roller and do you know any plans to build a rolling lunchbox planer stand or cabinet.
I have the HD ridgid 12" planer. So I guess a better question is how often should I change blades in jointer and planer and maintenance my cheaper tools I use daily. To rid of snip and a seemingly guy crooked planer bed? Broken_pine
2) Hello everybody. First time listener, long time caller. Wanted to hear of any shop items you use that would be more "eco-friendly". An example that comes to mind is instead of using the disposable glue brushes using a silicone one. Thanks, Twin Lake Woodshop
Guy
1) My question is that I have two logs (from the same branch but non-contiguous), and need two nightstands, primarily composed of a 16" w x 14" h x 12" deep mitered box/case. One log is dead straight grain and the other, beginnings of a crotch. Aesthetically, would each of you combine the two logs to make two "truly" matched (well bookmatched) nightstands, or use one log for each nightstand, matching grain WITHIN the individual nightstands, but not BETWEEN the pair? That's confusing even reading it back so please contact me with any questions,
For reference the bed these will flank is a California king California king so there is a good deal of distance between them it's not like they'll be on on both sides of a twin. -Tom
2) Hey guys, from time to time I’ve been asking questions and you’ve always provided great advice. My question is, I’m tuning up my jointer and I have the tables co-planner within .002” out 18 inches from the cutter head. Is this close enough? Should I invest in a longer straightedge? Currently I’m using a 24” ruler from a good combination square. Looking online for straightedges, the Starrett 36” is $247.50 and it accurate within .0002”. I also found the Veritas 38” aluminum straightedge for $44.90 and is accurate to .003”. How strength of a straightedge do I need? And can I get away with an aluminum straightedge? Thanks so much for your thoughts. -Mike Gitberg
Huy
1) I am a newbie in woodworking! and I'm working on my indoor stairs to the second floor. Stairs are completely removed and we plan to have an open riser 3 1/2" thick tread. I have somebody who confirmed the structure and adapted it to city codes for me. So nothing dangerous is happening here.
I am trying to get the costs down while I like the walnut looks and because of that I am thinking of ripping and altering grain on 2"x12" nominal lumber from the big box store and making 3" x 11½" x 37½' butcher block of yellow southern pine (construction grade, kilin dried) and veneer it with 1/4" walnut.
I am buying a 16' 2x12 kiln dried yellow southern pine and will start ripping it after stocking it for a month in my garage.
Should I be worried about wood movement? I mean movement between walnut and SYP. I am not worried about SYP core because I have one of them made two month ago and it's been staying inside with us and cupping/twisting, has not been observed.
Will the 1/4 glued walnut veneer is a good idea for this application in term of resisting wear and tear?
I am using regular glue for making the core. any advice on glue for making the core and veneer?
Will you approach same method to do this project? If not, What will you do? vafa
2) G'day team
It's the old guy (older than Guy) from Australia who potters around in the shed in his thongs ( Aussie footwear Guy )
I recently bought a Dewalt 735 thicknesser because I like to use reclaimed wood but I really don't have a clue what I am doing but you need to start somewhere.
Anyway I recently used the thicknesser on a couple of large pine blanks that came from some sort of industrial packaging which were approx 5 inches wide and 3 inches tall ( I used imperial for you guys)
I ran both blanks through the thicknesser " jointing" one side first by using a planer sled and some shims and then running the other side through squaring up the sides to each other and then gluing both pieces together to make a blank for a bandsaw box, everything seemed good at this stage.
I started to cut the blank on the bandsaw only to realise that it wasn't square to the table and that I had actually made a square block that was tilted ( I think it's called a parallelogram, I wanted to use a big word so Huy would feel at home)
How can I square this up ? The block is approx 5 by 5 inches and my table saw height is 3 inches.
I probably did this all backwards but even though I'm old enough to remember dust being invented I still like to learn.
Do I need to buy a jointer ?
Thanks for your help (ps, the nurse is cranky with me because I took some other guys slippers and won't take my medication, hope you guys get this while I'm still alive.........still no Sawstop) -Geoff
No comments yet. Be the first to say something!